Construction of industrial refrigerating chambers
Industrial refrigerating chambers are an important element for many industries, in particular in the food, pharmaceutical, and logistics industries. They ensure reliable storage of products at low temperatures, which helps to maintain quality and increase the shelf life of products. The construction of such cameras is a complex process that requires a professional approach, knowledge of technologies and strict compliance with regulations.
Stages of construction of industrial refrigerating chambers Designing. This stage is one of the most important, because it is the project that determines the efficiency, size and technical characteristics of the future camera. Specialists take into account the features of the products to be stored, the required temperature regime, the volume of the chamber, as well as the specific requirements of the client. The equipment connection scheme and the location plan of the refrigeration system, which optimizes energy consumption, are being developed.
Selection of materials. Materials that provide reliable thermal insulation are used for the construction of industrial refrigerating chambers. Most often, these are sandwich panels filled with polyurethane foam or mineral wool. The thickness of the panels depends on the temperature conditions of the chamber - freezers require thicker panels that are able to maintain low temperatures.
Installation of the structure. After the design and selection of materials, the frame is assembled and the sandwich panels are installed. This process involves precise sealing, which is critical to avoid cold loss and reduce energy consumption. The camera must be completely isolated to avoid the influence of external factors.
Installation of refrigeration equipment. At this stage, refrigerating units, condensers, evaporators and other equipment are installed. The cooling system is selected depending on the required temperature and volume of the chamber. Most often, modern installations with the functions of humidity control and maintaining a stable temperature are used.
System automation. For ease of operation, refrigerating chambers are equipped with automatic temperature and humidity control systems. They help ensure a stable microclimate and promptly respond to any deviations in work. This is especially important for food and pharmaceutical products, where the smallest changes can affect the quality of the products.
Testing and commissioning. After installation of the camera and installation of the equipment, test runs are carried out during which all systems are checked, including tightness, operation of refrigeration equipment and automatic systems. After successful testing, the camera is put into operation.
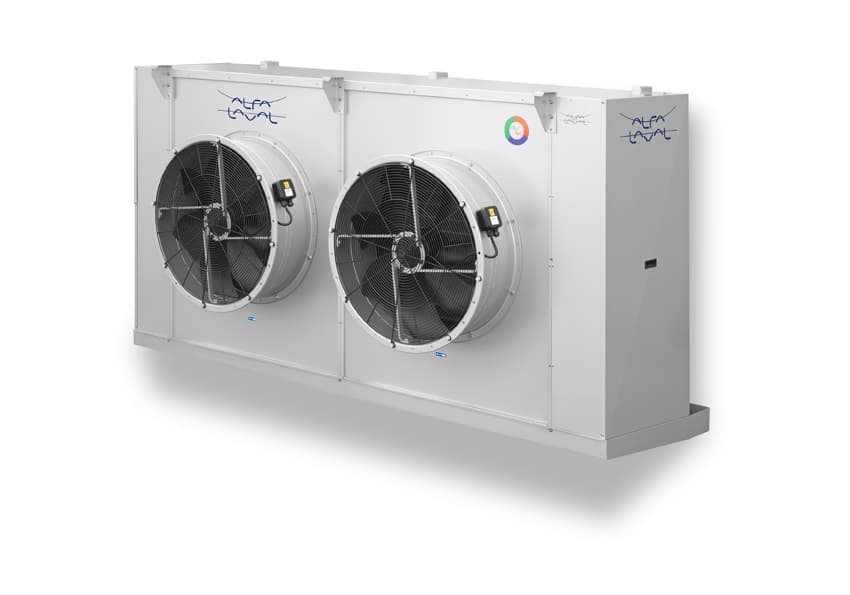
Quick calculation of the cost of installing an industrial refrigerator or freezer